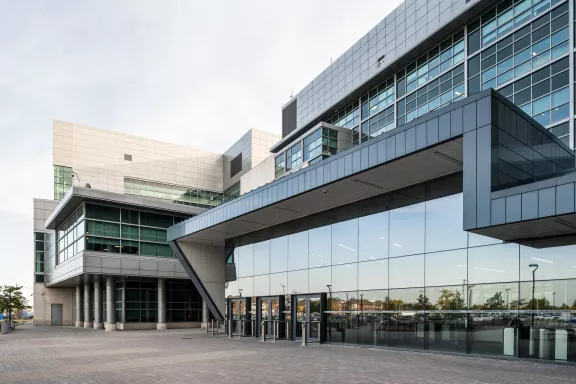
Catalyst is a Life Science and Research building developed by Seeker Labs. This seven-storey concrete structure, currently under construction, is located on Wade Avenue in the growing Junction neighbourhood of Toronto. Once complete, it will offer 155,000-sq.-ft. of best-in-class research and innovation space and will be leased to best-in-class life science research companies.
The building is being constructed on a site between the Lansdowne subway station and the Bloor GO and UP Express station.
BIM has been used extensively on this project for clash detection and constructability, allowing the project team to see issues prior to building and enabling significant cost savings for the client. Value management is being used to ensure the budget and design are aligned.
Drone photography is used for monthly reports and time lapse videos are capturing the progress of the work.
Project planning rests on a full loss planning system within the LEAN Construction approach. Methodologies for collaboration with trades allow visibility of every aspect of the project.
Another innovation that Pomerleau developed for this project is a custom-designed shoring system to hold the soil, limiting the number of permit authorizations required.
Shoring systems usually use tiebacks that often encroach into neighbouring properties. We redesigned it so that the tiebacks are either located on the property or use rakers that brace the wall inside the property.
“Shoring systems usually use tiebacks that often encroach into neighbouring properties,” explained Project Manager Sean Giblin. “We redesigned it so that the tiebacks are either located on the property or use rakers that brace the wall inside the property.”
Pomerleau’s design-build experience has been brought to bear on this project. While the project is being executed under the construction management contract method using a Dialog design, the team has been heavily involved in design aspects to ensure the building is as performative as possible while meeting budget conditions.
Our expertise in managing construction in tight spaces is an asset on this project. Given the access points to public transit, there is constant pedestrian traffic, in addition to the fact that adjacency to the TTC subway tunnel poses challenges that must be carefully managed.
Because the building is a concrete structure, Pomerleau’s experience with complex formwork is a great advantage. Project Manager Sean Giblin and Superintendent Sean Berridge bring a strong formwork background to the project.
This project is seeking LEED® Gold certification, and the building systems have been designed with the potential of converting them to net zero operations in the future.
One of main challenges on this project is the tight schedule. “Construction had to start prior to the completion of the design, this allowed us to move ahead with sequential tendering, which meant we could begin certain aspects while waiting for design completion,” said Giblin
The design not being fully completed also led to applying Conditional Permit Process to allow expedited mobilization. Also, because construction of the building is taking place five metres from the TTC tunnel between the Lansdowne and Dundas West subway stations, permits also needed to be approved by additional authorities.
Because the project site is in a tight space in a congested area for traffic and pedestrians, site logistics must also be tightly managed while keeping health and safety top of mind.
14,000
8,000
5
150