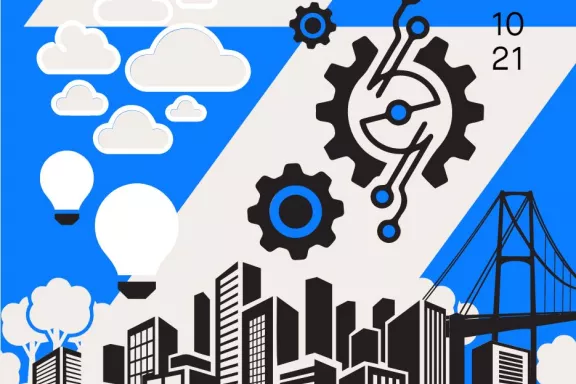
By Carolyne Filion, Director of Innovation - Research and Development, and Vincent Melanson, VDC Senior Integrator
Like a Lego model, a prefabricated building is made up of several components such as panels, modules, and/or units. Combinations of these components provide endless customizations to fit project’s needs and compared to traditional construction, the equivalent or superior quality is achieved. One of the main benefits of prefabricated projects is the possibility to pick and choose the building components from modular units to single wall panels, and anything in between. To better understand prefabrication, here’s a deep dive into the types of methods available on a project.
Figure - Example of various methods of prefabrication
Prefabricated components are standalone items that are usually associated with traditional construction methods which are manufactured and/or pre-assembled in a factory to improve the construction process on-site. Thereby, prefabricated components can be used in traditional construction projects to accelerate certain portions of work.
There are two main types of prefabricated components, MEP elements and subassemblies. MEP elements refer to mechanical, electrical, and plumbing elements and often consist of overhead racks and mechanical risers for main corridors or skid-mounted equipment for mechanical rooms. Sub-assemblies refer to prefabricated items included in a project, such as pre-assembled stairs, trusses, and precast concrete beams and columns. Mass timber components are beginning to gain in popularity.
As mentioned before, prefabricated panels can be customized as interior partitions, exterior façades, or any type of slab, and they can be designed to meet any specification required by building codes. The panels might be assembled with or without finishes according to project needs. Whether designed as light gauge steel, non-loadbearing, structural concrete, or heavy gauge loadbearing walls, prefabricated panels are best suited for projects with repetitive floor plans and common layouts such as mid- and high-rise residential, commercial projects, and large warehouses.
Modular pods are fully assembled units of usable space designed according to usual specifications and standards that traditional construction requires. Pods arrive fully finished – plumbing and electrical – on site and ready to be installed in the building. Usually designed for bathrooms and kitchens, modular pods are a good option for hospital, student housing, hotels, and residential projects where multiple bathrooms and kitchens follow the same design and configuration.
Generally, modular units are fabricated individually in a factory and delivered on site for integration into the project. After manufacturing is complete, the modules are transported on site then set on the foundation by a crane and connected to form the building. Modular units can also be integrated into an existing building structure to complete different sections of the building. The same as modular pods, modular units are usually fully finished, depending on the project requirements.