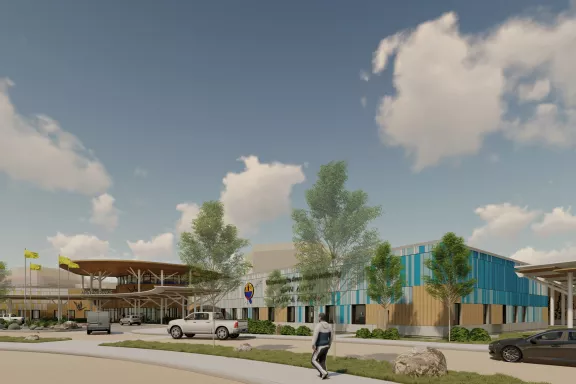
We’re proud to partner with Infrastructure Ontario and the Weeneebayko Area Health Authority and help First Nations communities receive emergency, and acute and specialty healthcare services in a modern, state-of-the-art facility.
Based in northern Ontario, the WAHA redevelopment project involves the construction of a new acute care hospital, Elder Care Lodge, visitor hostel and staff accommodations in Moosonee and a new ambulatory care centre on Moose Factory. Once complete, these modern facilities will support WAHA in providing exceptional, culturally-appropriate healthcare to patients and clients living along Ontario’s James Bay and Hudson Bay coasts, the majority of whom are proudly Cree and hold a strong connection to the land and waters that are their traditional territory.
The project aims to achieve LEED v4 Silver Rating certification in Healthcare, with an emphasis on sustainable, environmentally-friendly materials. Environmental considerations will be incorporated through the implementation of erosion and sedimentation controls; integration of energy-efficient HVAC, electrical, and water systems to remedy increases to the building’s footprint; and enhanced indoor air quality measures. Architectural elements have been included in the design to allow ample natural daylight to foster a vibrant and energized environment.
This project will employ modular construction, prefabricated components, and advanced technologies like BIM 3D modeling, virtual reality, and drone imaging to streamline building processes. Innovations such as vibration detection sensors will also help minimize site disruptions. These approaches enhance efficiency and reduce the environmental impact.
Modular construction offers significant advantages for building hospitals in remote regions where infrastructure is limited. It allows for much of the construction to occur off-site in controlled environments, reducing the impact of harsh weather and minimizing on-site labor needs, which is crucial in areas with no paved roads or limited access. Modular construction accelerates the building process and ensures consistent quality, enabling faster delivery of critical healthcare facilities in challenging locations.
Engagement with the Indigenous communities and people in the region is a critical part of the collaborative approach Pomerleau is taking to ensure we listen to and understand the unique needs and interests of the Cree people. By respecting cultural practices and creating opportunities for local employment and skill-building – we’re fostering trust and building stronger relationships with Indigenous communities on infrastructure development. This approach not only advances reconciliation but also leads to more successful, sustainable projects.
Moosonee is accessible by air, rail and ice road. Helicopters are used between Moosonee and Moose Factory during the seasons when the ice road is not available. The remoteness of the build locations presents transportation and logistics challenges. Additionally, there is limited accommodations in the region, requiring the construction of a temporary workers camp.
The remoteness requires careful planning around weather conditions, which are not typical considerations in more urban or accessible projects. Design considerations have been thoughtfully made to reduce dependency on weather-dependent construction methods and maximize the use of prefabrication and modular buildings. Since the region experiences extreme cold and seasonal access restrictions, we’ve had to develop detailed contingency plans to keep the project on track.
The local municipal infrastructure will require upgrades to meet the needs of the future health campus. Additionally, a dedicated rail spur has been created to support material delivery.
419,311
4,206
1,659
400+
Pomerleau recognizes the opportunity for economic reconciliation the WAHA Redevelopment Project represents for the W6 Communities: Attawapiskat FN, Fort Albany FN, Kashechewan FN, Moose Cree FN, MoCreebec Eeyoud and Weenusk FN. Read more about how we are actively supporting the inclusion of the W6 Communities and W6 Businesses across the project through our Indigenous Participation Plan (IPP): English | Cree
If you would like to get involved in the project, please visit BuildingConnected for upcoming partnering opportunities. If you require assistance accessing BuildingConnected, please refer to our step-by-step guide.
Each month, we share highlights from our ongoing engagement with the First Nations communities connected to the Weeneebayko Area Health Authority (WAHA) Redevelopment Project. From community-led events to engagement sessions, we’re committed to listening, building trust, and working in partnership to deliver this healthcare campus.